减少往复式压缩机润滑油消耗
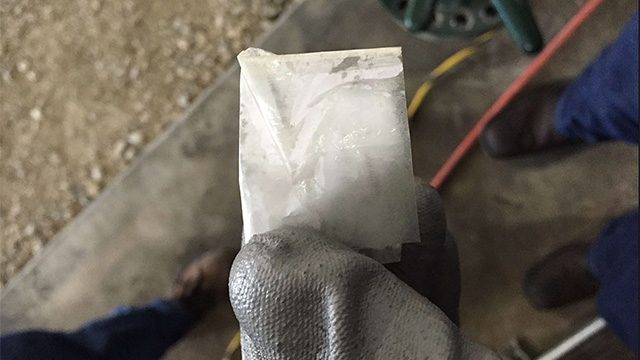
作者:美国俄亥俄州芒特弗农,Ariel 公司 - 贾斯汀·扬斯和乔·哈根
摘要
在北美运行的数万台往复式压缩机,每台每年消耗的润滑油费用高达 250,000 美元。通常,多数压缩机消耗的润滑油多于必要值,因此运行成本可以大大降低。通过相对简单的步骤来确定输送到每个润滑点的正确类型和数量,而不改变磨损部件的设计或材料,可以实现成本降低。本文介绍了所建立的方法,以及确保润滑系统正常运行的步骤,为压缩机长期可靠运行提供了依据。
引言
保持往复式气体压缩机的适当润滑对设备的可靠性至关重要。压缩机通常连续运行,则磨损部件会积累大量运行时间。往复式压缩机依靠两个润滑系统将润滑油输送到传动系统、气缸和填料中的关键部件。第一个系统是再循环系统,用于保护传动系统中的轴承、衬套、止推板和十字头。第二个系统是“全损耗”系统,为气缸内壁、活塞环、活塞杆和填料环提供润滑油。这两种系统的主要区别在于如何使用润滑油。在更换此油之前,传动系统会多次重复使用润滑油。气缸润滑系统在压缩过程中消耗润滑油之前,仅使用一次润滑油。在气缸润滑系统内有效使用润滑油是最大限度降低运行成本的同时实现设备可靠性最大化的关键。本文介绍了维持气缸润滑系统并确定适当润滑率的建立方法。
气缸润滑系统又名“强制注油”系统,它使用正排量柱塞泵给分配阀注油,分配阀将润滑油按比例分配至气缸和填料内的关键区域。关键区域的油流量近似于每分钟的油滴数。润滑油必须在足够的压力下输送,以克服每个关键区域的气压。这些压力通常在接近大气压到 3,000 psig 的范围内。润滑油注入关键区域后,润滑油将迁移至低压区或与流经压缩机气缸的气体混合。1,000 马力的压缩机每年可消耗 2,000 加仑的油,而较大压缩机每年消耗接近 6,000 加仑。考虑到矿物油每加仑的价格为 7 美元至 15 美元,合成润滑剂每加仑的价格为 20 美元至 50 美元,一台压缩机的年耗油费用可达 250,000 美元。此项年度费用并未涉及收集、运输和处理压缩机下游润滑油的相关费用。这些额外费用会大大增加与压缩相关的年耗油费用。
设计考量因素
往复式气体压缩机的应用范围很广。压缩机制造商需要评估每种应用的详细信息,以确定最坏的运行情况,以便可以推荐润滑油类型和润滑率。通常“最坏情况”是指具有最终阶段最大排气压力的运行情况。推荐的润滑油类型基于注油到气缸润滑系统每个关键区域后的预期粘度损失。润滑油粘度受气体组分、清洁度、压力和工作温度的影响。通常,较重的烃类气体和较高的排气压力会使气缸润滑油稀释,从而导致粘度降低和薄油膜保护成分形成。为避免粘度损失过多,建议使用较重的 ISO 级矿物油或耐稀释的合成润滑剂。
液体污染物(例如水、碳氢化合物)和缺油也会通过降低润滑油粘度和/或去除油膜而影响油膜质量。润滑不良会导致温度过高,从而降低部件寿命。在极端情况下,热失控状态可能导致部件迅速失效。
润滑率决定了在气缸润滑系统关键区域加油需求的频率。压缩机 OEM 已经有了自己确定润滑率的方法。Ariel 以一个“基础注油率”开始,范围在零部件直径的 0.3 至 0.5 品脱/天/英寸之间(计算示例参见附录 A)。压缩机机架的尺寸决定了使用的基础注油率。润滑率通过“基础注油率放大器”进行改变,具体取决于排气压力和气体组分。基础注油率放大器范围在 0.5 和 3 之间,具体取决于工作强度。该计算确定以机架额定转速运行的部件的“正常”润滑率要求。以较慢的转速运行将按比例减少(以半速运行时,在额定转速下需要“正常”润滑率的一半)。在压缩机运行的前 200 个小时,建议使用“磨合”润滑率,将注油量增至“正常”值的 150% 至 200%。额外的磨合油有助于冷却部件,并在部件相互贴合时冲洗磨损碎屑。
在多数情况下,考虑到某些未知或恶劣工况,推荐的气缸润滑率和润滑油类型会较为保守。润滑建议是根据将应用分组到一般气流类别中得出的。两种应用可能具有相同的类别,但在实际情况下对润滑油的侵蚀程度不同。根据工作强度,通常在磨合期结束后会预期减少一定量的润滑率。当气缸润滑系统尺寸适合一组“估计”情况的压缩机时,其润滑油类型和润滑率可能会严重不足或超出其实际情况。在某些情况下,这可能会影响分配阀选择、强制注油泵选型,并且如果推荐的润滑油也不能用于压缩机机架,则需要独立供油。
必须注意的是,填料可以根据压缩机应用而产生不同的热量。由填料产生的额外热量可保证增加推荐的润滑油粘度,以抵消在升温时的粘度损失。大量的热量产生需要用水或在某些情况下用油冷却填料,以保持合理的工作温度。
润滑减少的考虑因素
许多因素都会影响润滑率要求以及润滑油如何可靠地输送至气缸润滑系统的关键区域。以下是在改变润滑率前需要考虑的最常见因素:
润滑率因素:
- 气体组成和质量
- 压缩机运行速度
- 气缸润滑系统的润滑油类型和粘度等级
- 零部件几何结构(例如气缸内壁尺寸)
- 气缸排气压力
- 工作温度
- 强制注油泵和分配阀选型
- 润滑油饱和的循环气体
- 停用气缸操作
- 频繁启动/停止操作
润滑油输送因素:
- 强制注油泵和分配阀孔/活塞磨损
- 安装和平衡阀选型
- 将润滑油管线布置正确至/自分配阀
- 泄漏 — 连接、丘宾管、接头、O 型圈损坏
- 润滑部件磨损和几何结构变化
- 供油(高位油箱)输油管线布局
- 管线选型以改善油流量
- 伴热以改善油流量
- 过滤以改善油质量
- 单向阀故障
在继续降低润滑率之前,需要复核当前的压缩机设置。可能发现在最初确定气缸润滑系统选型时已开发或未考虑的因素。在降低润滑率之前,气缸润滑系统的设置必须正确且认为工作状况良好(可靠)。在降低润滑率之前,系统的组件使用寿命和性能应满足要求。
气缸润滑系统通常针对特定的“最坏情况”压缩机工况或应用设定尺寸。系统需要承受压缩机在使用中将遇到的最困难的应用。根据设备的使用年限或机组大小,气缸润滑系统可能无法再正常运行,或无法根据压缩机应用设定尺寸。可能需要更新气缸润滑系统的硬件和润滑油表,以便可以获得合适的启动润滑率来满足当前操作条件。
必须有条不紊地减少润滑率以避免润滑不足的情况,否则会因为工作温度升高而意外损坏部件。温度过高可能导致活塞/填料环以及活塞杆和气缸内壁等其他主要部件损坏。部件故障可根据其严重性而产生巨大成本:
- 人工(加班)= 2,000 美元/天
- 填料和活塞环更换 = 3,000 美元
- 加急发运 = 4,000 美元
- 气缸更换 = 25,000 美元
- 产量损失 = 40,000 美元/天
减少过程要求缓慢地降低润滑率,并在每次减少后进行定期检查。这将验证部件上的油量和质量。边界润滑的证据表明润滑率何时需要增加。由于填料盒的构造方式,很难检查填料内的油膜。对于这些部件,可以监测排气管线泄漏和/或管道接触温度,以记录工况的变化。需要一致的管道位置(最接近填料盒)和用于验证接触温度的方法。
磨合润滑率
当新的环部件在运行的前 200 小时磨合时,会补充润滑油。磨合期结束后,必须手动将润滑率从“磨合”率降低至“正常”润滑率。改为正常润滑率通常可减少 33% 至 50% 的油耗。某些设备可能会在不经意间以磨合率长时间运行,因为磨合期后润滑率从未降低。
润滑减少前的检查
必须确定与活塞环、承磨环和填料等部件的加速磨损相关的任何历史记录。磨损部件的相关问题可能导致对故障模式进行进一步调查,并可能导致在进行进一步调查之前暂停任何润滑减少。
为帮助识别由强制注油润滑系统润滑的部件上的任何加速磨损,应进行彻底检查。要记录的参数:
- 停机之前测量的填料泄漏/排气温度
- 活塞杆直径
- 活塞环/承磨环环槽宽度/深度
- 气缸内壁内径
- 与填料杯深度有关的填料盒尺寸
- 活塞环径向厚度、宽度
- 承磨环径向厚度、宽度
- 显示所有级数气缸内壁润滑质量的卷烟纸测试
- 应检查强制注油润滑系统,以确保其运行良好。这应包括分配阀压力测试。
初始检查和进一步检查所需的工具:
- 测量填料泄漏的气体流量计
- 监测填料排放/排污温度的温度测量仪器
- 游标卡尺
- 外径千分尺,适用于所有活塞凹槽直径
- 内径千分尺或量缸表,适用于气缸内壁直径
- 深度千分尺
- 未打蜡的卷烟纸
在测试前收集所有信息后,可以检查应用,以确定其是否合适进一步减少润滑。如果所有检查都显示机组未出现过度磨损,并且显示所有磨损部件均具有良好的润滑质量,则可以制定并遵循润滑减少步骤。
现场润滑减少步骤
确定某一应用是润滑减少的良好选择后,就必须制定相关步骤,以确保对所有强制注油部件正确应用润滑并密切监测参数。要确定所有部件的润滑情况,必须定期进行检查。这些检查包括:
- 气缸润滑试纸测试
- 该测试通过将润滑油从内壁上转移到未打蜡的薄层卷烟纸来估计气缸内壁上存在的油量。
- 应在机组停机后的一小时内进行试纸测试,以呈现运行期间最佳的气缸润滑油膜。测试步骤如下:
- 施加轻微压力,用两层普通未上蜡卷烟纸一同擦拭气缸内壁。从顶部开始,沿气缸内壁圆周以 20° 夹角(介于 1/4” 和 4-5/8” 之间,具体取决于气缸内壁)向下擦拭。贴着气缸内壁表面的那层纸应着色(被油沾湿),但第二层纸不应被浸透。
- 在气缸内壁两侧端重复执行此测试,以大约 90° 夹角从顶部开始,每侧均使用两层干净的纸。如果贴着气缸内壁的那层纸并未染透,则可能说明润滑不足;如果两层纸均已染透,则可能说明润滑过度。
- 填料泄漏
- 填料泄漏流量是填料环密封效果以及密封表面是否磨损或损坏的指标。
- 测量填料排放/排污的填料泄漏,以监测气体泄漏增加。这可以使用便携式或永久性气体流量计完成。
- 尽可能靠近十字头滑道来测量填料排放温度。该测量将指示是否发生增加的填料泄漏。如果使用红外测温仪器,请务必考虑测量表面的发射率和面积。需要测量新填料的基准温度以确定泄漏量是否增加。
- 目视检查气缸内壁、十字头滑道隔室和活塞杆
- 磨损的滑动表面可加速环磨损并提高泄漏率
- 目视检查气缸内壁和十字头滑道隔室,以确认是否有磨损材料从部件上磨掉了。
- 应目视检查活塞杆是否有划伤或过热迹象。
应按照下述时间间隔进行检查:
表 1. 润滑减少时间间隔
经过的时间间隔 | 总运行时间 | 从正常速率算起的总润滑减少量 [%] | |
---|---|---|---|
在磨合润滑率下启动 | 0 | 0 | |
磨合速率是正常值的 150-200% | |||
将系统设置为正常润滑率 | 200 小时 | 200 小时 | 0 |
查看状态 | |||
将正常注油量降低 10% | 1 个月 | 1 个月 | 10 |
停机进行检查如果满足要求,则进行下一步操作 | |||
将注油量再降低 10% | 1 个月 | 2 个月 | 20 |
停机进行检查如果满足要求,则进行下一步操作 | |||
将注油量再降低 10% | 1 个月 | 3 个月 | 30 |
停机进行检查如果满足要求,则进行下一步操作 | |||
将注油量再降低 10% | 1 个月 | 4 个月 | 40 |
停机进行检查如果满足要求,则进行下一步操作 | |||
将注油量再降低 10% | 1 个月 | 5 个月 | 50 |
停机进行检查如果满足要求,则进行下一步操作 | |||
将注油量再降低 10% | 约 6 个月 | 8,000 小时 | 50 |
停机进行完整检查 |
在 8,000 小时的测试以及上述检查结束后,还应拆下活塞总成,以检查活塞环槽、活塞环、承磨环、活塞杆和气缸内壁。测试开始时,应将所有尺寸与原始测量值进行比较,以确定是否有相当大的磨损。
在测试中的任意时刻,如果发生填料泄漏增加/温度升高或气缸内壁的润滑质量下降至边界状态,则不应继续减少润滑。如果气缸润滑不足,则应以 10% 的增量增加润滑,直到气缸表面恢复到正常的润滑水平。如果特定的润滑点出现边界润滑,则压缩机 OEM 可以重新配置分配阀布局,以根据试纸测试结果调整润滑油输送至特定点。理想情况下,所有气缸润滑点在内壁上都有足够的油,仅使一层卷烟纸浸湿。
附录 A:
Ariel 润滑率计算示例
Ariel 气缸/填料润滑油
基础注油率 ,直径为品脱/天/英寸
(升/天/毫米)(基于压缩机机架类别)
JG:A:I:M:N:P:Q:R:S:W 0.3 (0.0056)
JGH:E:J:ACF 0.4 (0.0074)
JGK:T:C:D:F:Z:U:B:V, KBB:V 0.5 (0.0093)
气缸润滑点
气缸内壁直径 X 基础注油率 X 基础注油率放大器 = 品脱/天
总润滑率将在一个气缸内壁上的多个润滑点之间平均分配。
填料润滑率
2 X 活塞杆直径 X 基础注油率 X 基础注油率放大器 = 品脱/天
对于带尾杆气缸,分别计算两个填料的润滑率。高压气缸 (> 3,600 psig MAWP) 的活塞杆填料使用两个润滑注油点。总润滑率将在多个润滑点之间平均分配。
建议的每天润滑率计算示例
JGJ/2,采用管道外输标准天然气(参见建议的基础注油率), 以下实际气缸内壁列示在气缸铭牌上,1.5 英寸(38.1 毫米)直径的活塞杆,使用矿物油润滑:
冲程 1: | 13.00”J(330 毫米)气缸,排气压力为 100 psi(6.89 巴)。基础注油率放大器 = 1 |
冲程 2: | 9.75”J-CE(248 毫米)气缸,排气压力 577 psi(39.8 巴),曲柄端。基础注油率放大器 = 1 |
冲程 3: | 5.125”J-HE(130 毫米)气缸,排气压力 1,636 psi(112.8 巴),缸头端。基础注油率放大器 = 1.25 |
气缸内壁填料润滑率计算
气缸内壁: | 13.00 英寸 x 0.4 品脱每天/英寸 x 1 = 5.2 品脱/天 |
填料: | 2 x 1.5 英寸 x 0.4 品脱每天/英寸 x 1 = 1.2 品脱/天 |
气缸内壁: | 9.75 英寸 x 0.4 品脱每天/英寸 x 1 = 3.9 品脱/天 |
填料: | 2 x 1.5 英寸 x 0.4 品脱每天/英寸 x 1 = 1.2 品脱/天 |
气缸内壁: | 5.125 英寸 x 0.4 品脱每天/英寸 x 1.25 = 2.6 品脱/天 |
建议的总量,品脱/天 = 14.1 品脱/天 |
注:
以上计算的速率是机架额定转速 (1,800 RPM) 下的“正常”润滑率。
在较慢转速下运行需要按比例降低润滑率。
在前 200 小时运行中,“磨合”润滑率将为“正常”润滑率的 150% 至 200%。
附录B:
现场润滑减少案例分析
设备:Ariel JGC/4,工作 49,000 小时
应用:集气
润滑减少目标值:正常润滑率的 50%
表2:机组工况
列 | 1 | 2 | 3 | 4 |
---|---|---|---|---|
压缩级 | 3 | 空白 | 2 | 1 |
吸气压力,psig | 450 | 不适用 | 215 | 92 |
排气压力,psig | 915 | 不适用 | 460 | 220 |
RPM | 1,000 RPM | |||
比重 | .59 | |||
应用 | 集气 | |||
正常润滑率 | 奇数侧 — 15 秒(22.5 品脱/天) 偶数侧 — 10 秒(26 品脱/天) |
|||
润滑率目标值(正常的 50%) | 奇数侧 — 30 秒(11.2 品脱/天) 偶数侧 — 20 秒(13 品脱/天) |
执行摘要
为了不断改进产品并收集数据,Ariel 与一名终端用户一起工作,减少他们其中一台集气压缩机在强制注油润滑系统中的润滑。目标润滑率是 Ariel 在初始压缩机选型时建议的正常润滑率的 50%。
在预定的时间间隔进行定期检查,以监测所有磨损件的填料泄漏、活塞杆直径和润滑质量。检查并测量了所有磨损部件,以确认是否有加速磨损。未发现异常磨损,且如果不是在 Ariel 的制造公差范围内,则大多是部件测量值均在磨损极限内。检查间隔使 50% 的润滑减少目标值成功到达。测试在最终检查后结束,机组重新上线,继续以 50% 的润滑减少量运行。
测试讨论
在 50,000 小时大修期间安装了新 Ariel 超低排放填料(B-7147、B-7109)。此时,还对气缸、活塞、活塞杆和填料进行了检查,以基本了解强制注油润滑在该应用中的运行方式。检查显示,强制注油润滑系统提供的所有部件看起来都涂满了大量润滑油(图 2、3)。根据对严重润滑过度系统的观察,忽略最开始 10% 的减少量并在首次减量时将润滑率降低了 30%。
在 658 小时的运行时间之后,再次进行检查以确认是否有任何异常磨损、填料泄漏,并使用卷烟纸测试来确认气缸内壁中的润滑质量。在检查期间,所有级数均不存在填料泄漏。每个活塞杆的外径都在填料区测量,以监测磨损情况。活塞杆是新的,并且安装时插入的原始剖面线仍然很清晰。每级的卷烟纸测试仍显示气缸润滑过度。基于这一信息,润滑率又降低了 10%,从设计上总体降低了 40%。
再过 988 小时后,根据测试计划再次检查机组,以检查填料泄漏、活塞杆磨损和气缸内壁润滑质量。所有检查均得到出色的结果,无测量的填料泄漏、无活塞杆磨损以及气缸内壁轻微润滑过度。根据此次检查,润滑率又降低了 10%,从原始设计上总体降低了 50%。
再过 1,137 小时后,自大修以来共运行 4,655 小时,根据测试计划再次检查机组。结果再次非同凡响,没有可测量的填料泄漏,也没有可测量的活塞杆磨损。这次,第 1 级和第 2 级气缸内壁出现轻微润滑过度,而第 3 级卷烟纸测试表明,该级润滑很完美。第一张卷烟纸浸透,但第二张试纸没有。至此,50% 的减少目标已经实现。因此,没有进一步减少润滑。
为确保压缩机组件的使用寿命可接受,再过 2,167 小时后,自大修以来共运行 6,822 小时,再次检查机组。该机组表现处与先前检查相同的特性,无可测量的填料泄漏,与卷烟纸测试的结果相似,并且活塞杆接近“崭新”。此时我们决定在减少量为 50%,接近 8,000 小时的时候,进行最后检查。
自大修以来的 8,668 小时并以 50% 的减少量运行 7,022 小时后,拆卸机组,以检查气缸内壁磨损、活塞杆/活塞磨损、填料泄漏和所有磨损部件的润滑质量。填料没有可测量的泄漏。
气缸内壁磨损测量完全在磨损限值范围内,并且在大多数情况下,均在制造公差内。活塞杆处于“崭新”状态,在测试中未出现磨损。活塞环环槽宽度与零部件的使用年限一致,并且与测试开始时的原始测量值没有明显差异。气缸和活塞杆的润滑质量与先前检查相似,并通过了卷烟纸测试(图 4)。
结论
最终的检查结果显示,润滑率降低 50% 并不会加速磨损或影响填料泄漏。可以合理地假设,使用具有相同应用和气体组分的姊妹设备可以实现类似的或至少显著的减少量。