通过设计原理排除压缩机故障
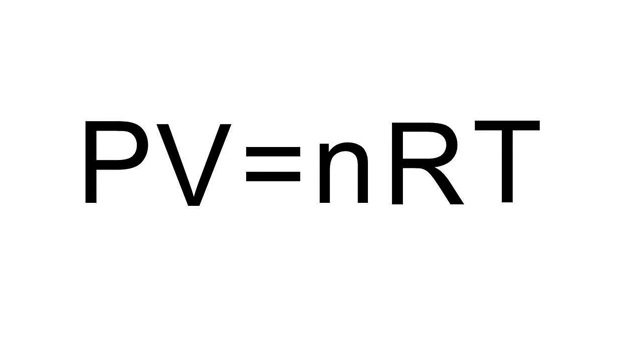
我们来看看设计部分。此部分内容将帮助您进一步了解统领设计流程的各种关系和一些常见问题点。然后,再通过这些关系来挖掘压缩机问题的根源。
了解基本的设计关系
在进入工程设计领域之前,必须先了解几个重要的物理关系。
理想气体定律
在压缩过程中必须计算和控制三项特性 – 压力、体积和温度。气体的这三项特性相互之间有着密切的关系。保持其中一个恒定,另外两个将成正比或反比。此类的理想气体定律包括:
- 波义尔定律(Boyle’s Law)。该定律是指,如保持温度不变,当体积减小时,压力就会增大。
- 阿蒙顿定律(Amonton’s Law)。该定律是指,如保持体积不变,当温度升高时,压力也会增大。
- 查尔斯定律(Charles’ Law)。该定律是指,如保持压力不变,当温度升高时,体积也会增大。
在测量压缩机中气体的体积时,必须使用在所有大气压力条件下都适用的标准立方英尺。德克萨斯州加尔维斯敦海滩上的环境气压大大高于科罗拉多州丹佛暴风雪时的气压。差异有一部分源于两地的相对海拔高度。另一部分与相对温度相关。很明显,海滩温度要更高一些。
标准立方英尺在几百年前被定义为测试气体体积的标准。规定的环境条件接近于冬季的加尔维斯敦海滩。如果我们坐于温度为 60°F 的海滩,则很可能不愿下海游泳。好,现在回来正题。在上述温度和压力条件下,如果我们将一个尺寸为 1 立方英尺的盒子打开放到海滩上,然后合上盖子 – 盒中就有了 1 标准立方英尺的空气。根据定义,形成 1 标准立方英尺空气所需的条件是 60°F 的环境温度和 14.7 PSI 的环境气压。
实际立方英尺对比标准立方英尺
愉快的海滩之旅后,我们来探讨一下真实世界的状况。如果我们将盒子带出海滩,并且将盒盖向盒内推进一半且不让空气逸出,那么盒中现在的空气体积则是 1/2 实际立方英尺。但盒中的空气体积仍是 1 标准立方英尺。区别在于同样的气体量但实际体积变成了 1/2,而压力和温度增加了。只有当环境条件是 60°F 和 14.7 PSI 时,气体的实际立方英尺和标准立方英尺测量值才相等。
为什么说了解气体在每级的温度和压力十分重要
如果将理想气体定律与标准立方英尺的概念相结合,就可以计算气体通过压缩机时的温度、压力和体积,而无需去海滩或挤盒子。海滩之旅听起来也许很美妙,但如果能在制造压缩机之前计算出压缩机将要执行的操作,就一定可以节省大量的时间和资金。
压缩机设计示例
本示例将引导您完成压缩机设计流程中的典型步骤。如果您知道如何设计机器来获取所需的输出,但实际操作之后却无法得到所需的输出,本示例可帮助您查找原因。
步骤 1 - 确定总压缩比
设计流程的第一步是通过系统的吸气和排气压力来计算总压缩比。假设入口表压力为 100 lbs,所需的最终输出表压力为 1,000 lbs。想当然的答案是 1,000 除以 100 得到总压缩比为 10。错。请记住,上述数字均为表压。我们必须要使用绝对压力值。这意味着要在表压的基础上增加大气压力(海平面上为 14.7 lbs – 根据您所在的位置校正此值)。完成考虑到大气压力的校正后,再用最终压力值除以进气压力,得出总压缩比为 8.84。
这种总压缩比在实际应用中相当标准。集气应用将压缩比限制在每级 2.4 到 4.0。压缩天然气 (CNG) 应用从 5 lbs 开始,最高达到 4,600 lbs。另一方面,管道输送应用在单级机组中采用 1.05 到 1.2 的极低压缩比。无论是何种应用,计算总压缩比都是设计流程的第一步。
步骤 2 - 机组中有多少级?
有许多因素会限制单级可提供的最大压缩比。最重要的可能是活塞杆载荷和气体温度。要限制级数的原因包括尽可能提高传动效率(所需的传动机组大小/功率)和尽可能降低外围设备(冷热调节器、洗涤罐、控制和监视设备等)的成本。
还以上一步的内容为例。总压缩比为 8.84。鉴于所处理的混合气体的体积和温度限制,我们需要一个多级机组。因此,我们需要计算每级要处理的压缩比。如果是使用两级系统,则取总压缩比的平方根。8.84 的平方根为 2.97。对于三级机组,我们取 8.84 的立方根 2.06。对于后续级数的机组,则是取总压缩比的 n 次方根,其中 n 为级数。
在此应用中,设计限度是每级压缩比为 2.97。即使我们的两级与三级系统的气缸数目很可能一样,我们也要去掉一整套的冷热调节器、洗涤罐和控制电路而使用两级设备。如果主要问题在于温度,则三级机组的操作温度(和活塞杆载荷)更低,只是购买和操作成本更高。
步骤 3 - 计算气体温度
保持整个机组内的温度一致是确保正常运行的关键。在计算机组的总压缩比时,使用的是绝对压力。为了准确测量热特性,必须使用绝对温度。华氏温标通常用于测量室温。而绝对温度使用兰氏温标来测量。华氏温度加上 460 便可得出兰氏温度。之所以使用兰氏温标,是因为所有设计和气体定律方程式都取决于在绝对温标下测量的温度。
我们现在要找到每级的吸气温度。每级的吸气温度及压缩比与 n 值一起用于计算排气的不同特性。n 值是一个常数,随具体气体组分变化。这些常数在大多数机械工程参考书籍上都能找到。n 值代表气体比热。此比率可辅助描述气体在不同温度和压力条件下的体积。能够计算出某压缩机级的排气体积,对于确定下一级气缸的大小至关重要。如果不知道需要压缩的吸入气体的体积,就无法确定该级气缸的大小。
步骤 4 - 确定功率和机架规格
到此为止,我们已经做出了设计流程中的几项重要决定。总压缩比为 8.84,这可以将 100 lbs 的进气压力提升至所需的 1,000 lbs 排气压力。我们将使用每级压缩比为 2.94 的两级机组。此信息足够计算出传动机组所需功率了。确定传动机组大小后,即可为压缩机机组选择一个机架。
步骤 5 - 确定所需流量
流量有时以该机组每天可以压缩的立方英尺数来表示。每天流量的实际意指是什么?我们不妨再回到明媚的加尔维斯敦海滩。假设有一个能装 125 万立方英尺气体的巨大气球。假设它不会遮挡阳光,我们继续。如果我们将一台压缩机连接至此气球后打开,则可以通过抽空气球所需的时间来确定该压缩机的流量。如果气球在 24 小时内抽空,则压缩机的每天流量就是 125 万立方英尺。如果在 12 小时内抽空,则该机组的每天流量为 250 万立方英尺。
大多数压缩机的规格都是用每分钟(而非每天)的标准立方英尺数表示,即通常简称的 SCFM。如果有必要将每天流量换算为每分钟流量,只需除以 1,440(每小时 60 分钟乘以每天 24 小时)即可。
不过,压缩机内径尺寸的测量单位不是英尺,而是英寸。因此在表示气体输出体积之前,还需要将内径的立方英寸换算成立方英尺数。该图说明了每个活塞运动行程提供的大致体积。将此体积与曲轴的 RPM 相乘,即可确定气缸每分钟的输出量。双作用气缸要求将曲柄端位移与缸头端位移相加,再乘以 RPM,即可得出气缸每分钟的输出量。
步骤 6 - 计算活塞工作体积位移
计算气缸流量非常简单,对吧?实际不是的。几个因素决定了气缸的排出量永远不等于其总工作体积位移。活塞从来不会完全到达气缸内壁的末端。因为并未排出气缸中的全部气体,此余隙减少了气缸输出体积。另一个降低效率的因素是在进气阀打开前(为下一个压缩行程放入更多气体)活塞必须退入气缸的距离。这些主要因素加上其它几个次要的因素,即形成了一个所谓的容积效率数。要在理想输出体积的基础上加上气缸的容积效率,才能计算出实际输出体积。
在我们的设计示例中,则要使用每分钟 115.53 实际立方英尺的流量来补偿海平面高度和 80°F(加尔维斯敦多数情况的现实平均温度)下的温度和压力条件,才能得出所需的 100 lbs 流量。容积效率进一步减少了流量,而需要的最终活塞工作体积位移为每分钟 144.4 立方英尺。现在,我们可通过列出上述所有此类信息的 Ariel 数据手册中挑选出 JGA 机架。我们的流量基于 1,800 RPM 的传动速度。您将会看到,数据手册中列出了缸头端和曲柄端工作体积位移。只需将活塞直径乘以行程即可以得出。加入这两个数字,就会看到随附的图表中有我们需要的每分钟 144 立方英尺的活塞工作体积位移。
步骤 7 - 确定第二级的大小
我们通过气缸要压缩的气体体积确定了第一级气缸的大小。在确定第二(或任何其它)级气缸的大小之前,必须先计算前一级气缸输出的气体体积。根据理想气体定律,我们可以使用气体压力获取第一级输出的气体体积。而且我们还知道压力。将第一级进气压力与第一级压缩比相乘,即可确定压力。因为两级的压缩比都是 2.97,进气压力是 114.7 lbs(不要忘记在 100 lbs 表压的基础上加上 14.7 lbs 的大气压力),排气压力将是 340.6。
为了复核第二级的最终输出压力,我们用第二级的压缩比 2.97 乘以进气压力 340.6,所以最终的输出压力是 1011.5。这与目标压力 1014.7 非常接近。现在我们使用理想气体定律公式来计算第二级进气的气体体积。每分钟实际立方英尺数为 41.78。如果应用校正系数,包括容积效率,就会得出吸入容积为 52.2。然后我们在 Ariel 数据手册中找到此吸入容积的正确活塞工作体积位移。在此应用中,我们使用头端为 6-1/8 英寸且曲柄端为 3-3/8 英寸的 JGA/2。现在我们已根据操作要求确定了压缩机的大小。
通过设计技术查找问题
在此场景中,我们将检查存在问题的两级压缩机机组。第二级的初始输出压力为 360 lbs。现已降至 300 lbs。第一级的输出压力和温度都有增加。此现象可能已经持续数周,但如果是缓慢的变化,您又没有记录输出等级,那就一直注意不到。压力等级会指出有问题的位置,因为如果压缩机气缸出现问题,其移动的气体就会减少。在多级机组中,有问题的级通常只是那个输出压力增加的级。有问题的级与最终输出之间的连续级将会出现压力净下降。在我们所说的案例中,第一级很可能有问题,因为其输出压力增加了,而第二级的压力下降了。
在单级机组或压力没有什么变化的机组中,必须严格依靠温度来查找有问题的级或区域。在此场景中,第一级输出的压力和温度都有增加。因为温度和压力增加而总压缩比下降,表明排气阀有泄漏。当活塞退入气缸以吸入更多气体时,排出的热气体也会侵入气缸。这可以解释第一级进气中温度和压力的升高。第二级输出的压力降低,是因为部分进气通过气阀泄露到了第一级。
在了解了设计流程是要平衡各级压缩比之后,知道总压缩比,即可轻松计算出每一级的压缩比。用最终输出压力除以进气压力。即可得出总压缩比。然后取总压缩比的 n 次方根(其中 n 表示级数)。用进气压力(考虑到大气压力的校正)乘以第一级压缩比。以此数字作为排气压力的近似值,继续用相同的方法确定每一级的吸气与输出压力。然后通过表压引导来查找有问题的级。通过温度也可以发现问题。温度可能是低压缩与单级应用中唯一可用的工具。