压缩机减排技术
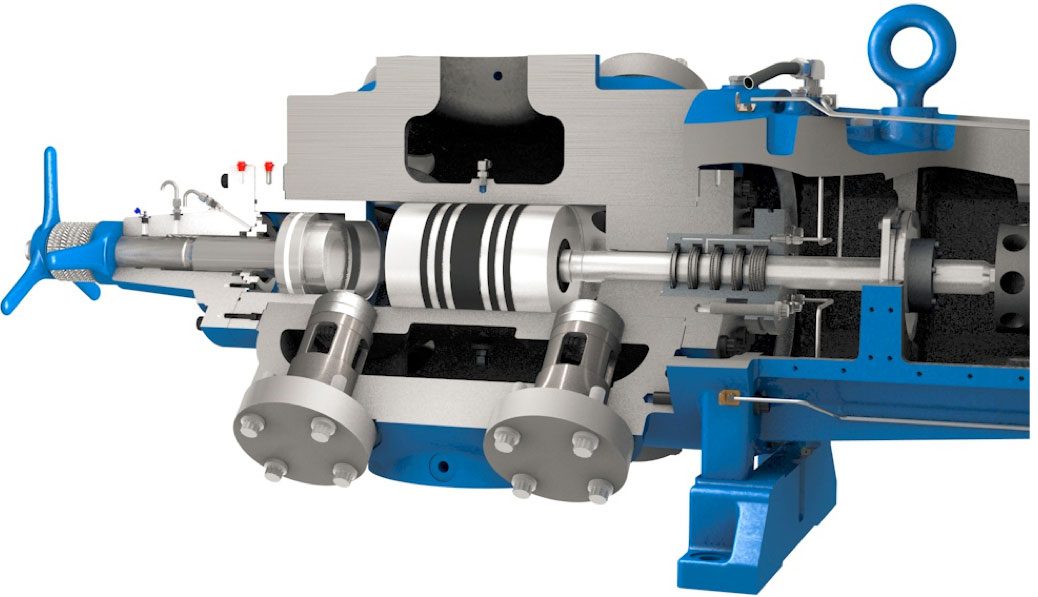
Ariel 公司,丹·汉农
往复式压缩机的气体泄漏不仅是产品损失。从环境、健康和安全以及区域分类的角度来看,向大气中泄漏气体也是一个问题。无论出于何种原因,最大限度减少甚至消除气体泄漏是所有制造商、操作员和往复式压缩机所有者的目标。有几种静态和动态密封可发生泄漏。
本文将从设计的角度讨论潜在的泄漏区域以及为消除或减少这些泄漏点而采取的措施。其重点是了解天然气行业已采取的减少或控制气体泄漏的措施。讨论的主题包括:
- 气体管道连接件
- 压缩机气缸阀盖
- 压缩机气缸头
- 卸料设备
- 活塞杆压力填料
- 回收或处理的收集
气体管道连接件
连接件和密封件的类型因尺寸和压力额定值而异。对于天然气工业中最常见的操作压力,采用 ANSI 型法兰。螺旋缠绕式金属垫片早已取代平面纸式垫片。螺旋缠绕式垫片的密封性能取决于法兰间的正确对齐。管道安装正确后,可消除这些法兰接头的泄漏。高压管道接头可以采用环型或透镜型接头连接件。某些较小的管线可能是带有压缩式接头的管道。无论连接件类型或大小如何,都必须遵循良好的装配规范。连接件必须正确对齐,避免撤消力将两个配合连接件拉到一起。气体泄漏检测方法可用于确认管道连接件的正密封。对热变化引起的管道膨胀的分析和考量将大大有助于减少管道连接件的受力和对中问题。
压缩机气缸阀盖
阀盖既可以接入压缩机气阀,又可以将气阀牢固地固定就位。多年来,阀盖设计不断发展,以提高气阀保持力和气体密封性。过去,阀盖用纸质垫片密封在气缸上。这种密封形式需要调整中心螺栓类型以将气阀固定就位。纸质垫片和中心螺栓都给维护无泄漏总成带来了挑战。O 型圈阀盖取代了旧的中心螺栓阀盖设计。O 型圈位于阀盖突出部的外径上,密封在气缸壁上。气阀保持力由阀盖螺栓维持。此 O 型圈密封提供了有效的密封,消除了阀盖的气体泄漏。必须遵循良好的维护规范,以确保定期更换 O 型圈。必须注意确保在安装过程中不切割 O 型圈。
O 型圈密封的设计必须考虑与压缩气体和用于气缸润滑的润滑剂之间的兼容性。在高压应用和特定气体类型中可能会发生爆发性减压。爆发性减压是由于放气期间气体渗入 O 型圈后迅速膨胀而导致的 O 型圈起泡或破裂。确认 O 型圈材料或 O 型圈凹槽直径可减少此破裂。
通过正确安装,O 型圈式阀盖密封设计可消除该接头处的气体泄漏。可使用气体泄漏检测进行确认。
压缩机气缸头
气缸头封住气缸的末端。缸头与气缸的接头是静态密封位置,通过正确的设计和安装可确保无泄漏。多年以来,在气缸到缸头密封设计中已用金属环型垫片取代了纸质垫片。通过正确的安装和维护,这些气密性密封可实现零泄漏。
气缸头螺栓对密封件施加夹紧力,并对气压保持力施加强度。这些螺栓承担了气缸的气体负荷。要避免将这些螺栓用于安装其他硬件,如垂直支撑。
卸料设备
卸料设备包括缸头端余隙腔、气阀卸荷器、阀腔和缸头垫块。卸料设备用于通过降低压缩效率或禁用气缸末端的压缩来减少流量或功率。卸料设备可以手动操作或气动操作。液压和电动设备较少见。
卸料设备将在执行杆处引入附加的泄漏路径。卸料频率可以是每小时几次,或者每月一次。杆密封件需要静态型密封件,它必须允许间歇性操作。杆密封件设计多种多样,多年来已有所改变,以提供更好的密封能力和更长的密封寿命。通常,一对密封件之间有一个指示排气口。如果第一个密封件泄漏,排气口允许通过受控的排气管线捕获气体。通过适当的安装和维护操作,卸料设备杆的泄漏有望为零。
活塞杆压力填料
活塞杆穿过气缸头进入压缩机机架。在天然气分体压缩机上,活塞杆以 3 英寸至 8 英寸的排量(冲程)和以高达 1,200 fpm 的平均速度进出气缸。压力填料盒有助于密封活塞杆。压力填料密封件的设计可尽量减少气体泄漏并将泄漏引导至安全处理或收集点。压力填料是动态密封,因此当密封件磨损时,甚至在安装新密封件时,也会产生气体泄漏。
多年以来,我们已应用各种设计。一些改进解决了固定密封表面的问题,但在解决填料环和活塞杆之间的主泄漏路径方面,几乎没有取得重大进展。这里将讨论最近的一项改进 — 整体环技术。
典型的填料环设计是在填料盒内使用多组串联的环。这些环组可能包括一至三或四个环。环通常被分割成三段,有不同的切割模式。它们与围绕在每个环外径的环状螺旋弹簧固定在一起。应用切割模式是为了在环磨损时保持活塞杆与环的接触。切割模式的不同是用于确保连续环的间隙不对齐,从而使泄漏最小化。在填料使用寿命内导致泄漏量的两个因素包括环分体之间的泄漏和活塞杆接触处的磨损。磨损寿命很大程度上取决于气体中的碎屑量和接触摩擦的热量。
整体环设计是三到四个环组,其中通常两个环是分体设计,两个环是实心设计或整体设计。在低压情况下,整体环与活塞杆之间保持的余隙非常小,其中一个环的余隙略小于另一个。在运行中,当通过压缩冲程的压力增加时,压力的增加会使第一个整体环负荷,将气体封闭到活塞杆并密封紧密。当达到全压时,第二未整体环负荷并密封至活塞杆。当压力通过活塞的吸气行程而减少时,这两个环将卸荷。
这种“必要时的负荷”可以实现非常紧密的密封,消除了传统分体式环在切口处和沿活塞杆发生的不均匀磨损泄漏。这也减少了密封环与活塞杆接触的总时间,减少了摩擦和热量。结果是活塞杆到环的温度越低,泄漏率越低。较低的温度直接与更长的使用寿命、更长的维护间隔时间有关。
在新的填料密封条件下,传统分体填料环的典型泄漏率接近 0.1 至 0.17 scfm。磨损环的泄漏率会增加,直到更换为止。为安排维护,“报警”点的典型速率接近每填料盒 1.7 到 3.4 scfm。(联邦排放法规未规定泄漏率,但是规定了更换填料密封环的总操作小时数。)
在新的条件下,报告的整体环设计泄漏率表现出相似且更低的数据率。由于摩擦热更低,随着时间推移,环的磨损更少,密封时间更长。在相同的运行时间内,泄漏率要低得多。
安装示例 1
一组 (7) 台 Ariel JGK/4 压缩机(2.0 英寸直径活塞杆)包括传统分体环和整体技术的活塞杆填料环。整体环比分体环“更持久”。整体环在运行 1 年至 1 年半后才会出现泄漏。在相同条件下运行的三个机组中,安装了整体环后,一个机组的泄漏最小,而另外两个在运行两年后仍未发生泄漏。
安装示例 2
一组 (12) 台 Ariel JGC/4 规格压缩机(2.5 英寸直径活塞杆),安装了整体环技术。运行的前四个月显示,每个填料盒测得的泄漏为 0 至 0.2 scfm。绝大多数测量值为零。
安装示例 3
几台 Ariel JGT/4 压缩机(2.0 英寸直径活塞杆),以 1,400 rpm 和 1,050 fpm 的活塞速度运行。压缩从 850 psi 到 1,130 psi
据报道,传统分体式填料环初始安装在新的和破损的情况下泄漏率很高。填料环已更换为整体环配置。初始填料泄漏显著降低。
最初安装的分体环显示平均每个填料盒的泄漏为 1.3 scfm。安装的整体环显示平均每个填料盒的泄漏为 0.035 scfm。将分体环更换为整体环后,活塞杆温度从平均 206 华氏度降低至 190 华氏度。
对安装的整体环进行跟进,提供了在 12,000 小时到 18,000 小时工作时间内 0.0 scfm 至 1.5 scfm 的测量数据。大多数填料盒在此工作时间范围内显示接近零泄漏。平均每个填料盒的填料泄漏为 0.094 scfm,平均工作时间超过 16,000 小时。
在六台机组达到 28,000 小时和 32,000 小时工作时间后,进行了最终跟进。在运行 3 年半至 4 年后,这 24 个填料盒的泄漏率显示,典型泄漏和磨损率显著降低。24 个填料盒的平均泄漏率为 0.45 scfm,最大单次填料泄漏率为 2.57 scfm。24 个盒子中有 14 个的可测泄漏为零。
典型报警点(计划维护时间)的预期填料泄漏在 1.7 到 3.4 scfm 之间。
收集或处理的布局泄漏
无论安装的填料设计如何,最终都会发生泄漏。如果由于环境或健康和安全原因无法将气体排放到大气中,则需要合适的收集系统。有各种不同的系统设计,可用于不同级别的密封。通过合理的努力和方法,可以最大限度地减少向大气排放的天然气。消除硫化氢等致命性气体的排放,需要更全面的放空系统。可以将一些功能和选项添加到往复式压缩机中,以适应所需的系统级别。其中包括不同的中体配置、吹扫气体功能和各种放空系统布局规划。在 API-618、GMRC 高速往复式压缩机橇指南和设备制造商指南中包含相关放空总管设计的讨论。
结论
天然气和二氧化碳被视为温室气体 (GHG)。EAP 指出,温室气体向大气中排放的增加会导致环境整体变暖。环保部门已开始就温室气体排放制定法规。目前,往复式压缩机的压力填料密封是根据工作时间而非整体泄漏进行调节。即便如此,减少泄漏仍是填料密封制造商和往复式压缩机制造商的关注点。
往复式压缩工业无闲置状态,从而可导致气体泄漏。在减少潜在排放方面已经取得长足进展。多年来,所有静态密封位置都已得到处理,如今已不被视为排放位置。动态密封位置(如压力填料盒)正通过新的理念和设计得到显著改善。可以非常有效地收集发生的泄漏,以便处理或重复使用。这是一个需要进一步监测和开发的议题。